Understanding Injection Molded Prototypes: A Key Asset in Modern Manufacturing
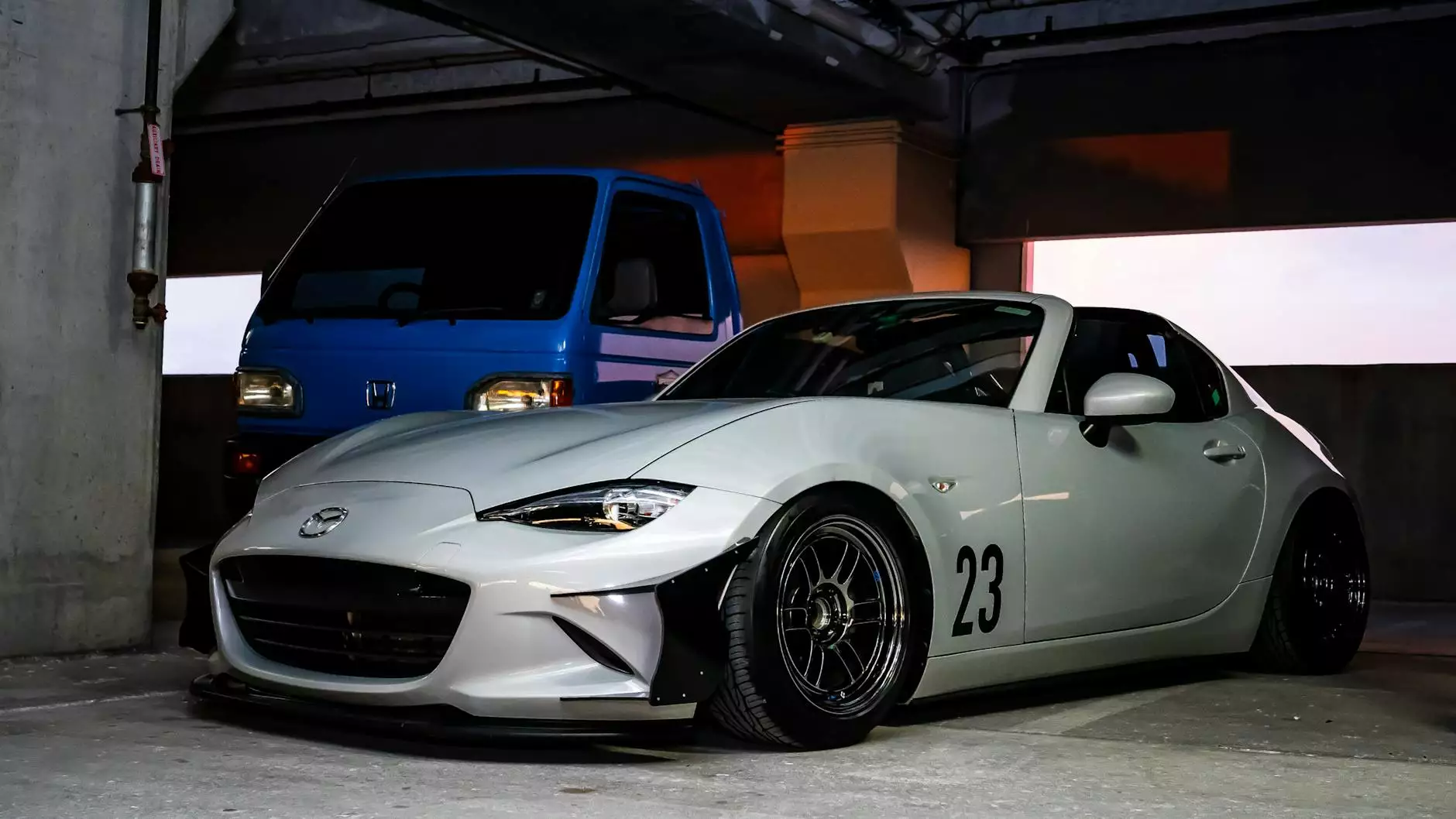
The realm of business is ever-evolving, and with advancements in technology, industries are continuously seeking innovative solutions to improve efficiency and reduce costs. One such groundbreaking approach is the utilization of Injection Molded Prototypes. This article delves into the significance, advantages, and applications of injection molded prototypes, showcasing why they have become a pivotal aspect of manufacturing today.
What are Injection Molded Prototypes?
Injection molded prototypes are preliminary models created to test designs and functionalities before committing to full-scale production. These prototypes are produced using the same materials and manufacturing processes that will be employed in the final product, ensuring that they closely mimic the performance and aesthetic qualities of the end item. The process of creating injection molded prototypes involves injecting molten material into a custom-designed mold, where it cools and solidifies, producing highly accurate and detailed parts.
The Importance of Prototyping in Business
Prototyping is an essential step in the product development lifecycle. It allows businesses to:
- Test Ideas: Assess the practicality and functionality of a concept.
- Identify Issues Early: Catch potential design flaws before full-scale production.
- Reduce Costs: Save money by making adjustments during the prototyping phase rather than after mass production begins.
- Enhance Communication: Provide a tangible representation that helps stakeholders visualize the final product.
Utilizing injection molded prototypes provides businesses with these advantages and more, as they facilitate a deeper understanding of product viability without the immediate need for large investments.
Advantages of Injection Molded Prototypes
When businesses opt for injection molded prototypes, they unlock numerous benefits that drive success:
1. High Precision and Accuracy
One of the primary advantages of using injection molded prototypes is the exceptional accuracy they offer. The process allows for intricate details that can be critical for parts that require tight specifications and tolerances.
2. Material Versatility
Injection molding can involve various materials, including metals, plastics, and even advanced composites. This versatility enables businesses to experiment with different materials that best suit their product requirements.
3. Quick Turnaround Times
With modern advancements in technology and processes, the turnaround time for producing injection molded prototypes has considerably decreased. This agility allows businesses to move swiftly from concept to testing, gaining valuable insights in a shorter timeframe.
4. Cost-Effectiveness
The initial investment in prototype development might seem significant; however, this approach ultimately saves money in the long run. By identifying flaws early and refining designs before full production, companies can avoid costly mistakes.
5. Realistic Testing
The ability to create prototypes that closely mimic the final product allows companies to conduct accurate tests. These tests assess how the product will perform in real-world scenarios, ensuring that it meets market expectations.
Applications of Injection Molded Prototypes
The applications for injection molded prototypes are vast and span numerous industries. Below are some of the sectors that benefit significantly from this technology:
1. Consumer Products
One of the most common applications is developing consumer products, ranging from kitchenware to electronics. Prototype testing ensures that these products are user-friendly and meet consumer standards.
2. Automotive Industry
The automotive sector heavily relies on injection molded prototypes to design and manufacture parts like dashboards, interior components, and even exterior fixtures. Testing these parts beforehand can enhance safety and functionality.
3. Medical Devices
In the medical field, precision is paramount. Injection molded prototypes allow manufacturers to produce intricate parts for medical devices, ensuring that they operate correctly and safely before entering the market.
4. Aerospace
The aerospace industry demands high-quality components that can withstand extreme conditions. By utilizing injection molded prototypes, manufacturers can test parts under simulated high-pressure and temperature conditions.
5. Industrial Applications
Various industrial products, such as machine components and tools, can be prototyped using injection molding. This process allows engineers to visualize and refine designs, improving efficiency in manufacturing.
How Deep Mould Excels in Providing Injection Molded Prototypes
At Deep Mould, we understand the significance of delivering top-notch injection molded prototypes. Our commitment to quality and precision ensures that our clients receive prototypes that meet their unique specifications. Here’s how we stand out:
- State-of-the-Art Technology: We utilize the latest machinery and technology to create precision molds that allow us to produce prototypes with unmatched accuracy.
- Expert Team: Our team of skilled professionals brings years of experience in metal fabrication and injection molding, ensuring the highest standards are met.
- Customization: We cater to specific client needs, offering customization options to suit various projects and industries.
- Quick Prototyping: Our efficient processes streamline development, allowing us to turn around prototypes swiftly without compromising quality.
Choosing the Right Partner for Injection Molded Prototypes
When selecting a partner for injection molded prototypes, it’s crucial to consider several factors to ensure you achieve the best results:
1. Experience and Expertise
Opt for a company with a proven track record in injection molding and prototyping. Their experience can lead to better solutions and insights for your projects.
2. Quality Assurance
Choose a partner who emphasizes quality control in their processes to ensure that prototypes meet your standards.
3. Technology and Equipment
Ensure the company invests in modern technology and equipment to produce high-quality molds and prototypes efficiently.
4. Flexibility and Customization
Look for a prototyping partner who is adaptable and willing to tailor their services to meet your specific needs.
5. Clear Communication
Effective communication is vital for successful collaboration. Choose a partner who keeps you informed at every stage of the prototyping process.
Conclusion
The role of injection molded prototypes in the manufacturing landscape cannot be overstated. They not only facilitate innovative product development but also provide businesses with the necessary tools to thrive in a competitive environment. As technology continues to evolve, so too will the methods and processes associated with prototyping. By embracing the advantages of injection molded prototypes, companies can ensure that they are well-equipped to navigate the complexities of modern manufacturing.
At Deep Mould, we are dedicated to helping businesses succeed by providing high-quality injection molded prototypes tailored to their unique requirements. With our expertise and commitment to excellence, we are ready to partner with you on your journey to success!